Статистика |
---|
Онлайн всього: 1 Гостей: 1 Користувачів: 0
|
|
32. Об'ємна штампування
§ 23. Технологія штампування на пресах
Штампування на кривошипних кувально-штампувальних пресах (ККШП). Ці преси є прогресивним видом обладнання, так як штампування на них в півтора-два рази продуктивніше штампування на молотах, точність штампування вище, витрата металу менше, а умови роботи безпечніше, ніж на молотах. Крім того, робота преса характеризується відносно невеликою швидкістю робочого ходу - до 0,5 м/с, відсутністю ударів і динамічних навантажень на фундамент і грунт. Тому монтаж пресів не вимагає споруди громіздких і дорогих фундаментів, а будівля цеху може споруджуватись полегшеного типу.Полегшуються механізація і автоматизація процесів штампування, так як ККШП успішно вбудовуються в потокові лінії (рис. IV.32, б). Завдяки зазначеним переваг у знову споруджуваних і реконструйованих ковальсько-штампувальних цехах зазвичай встановлюють преси, а не молоти.
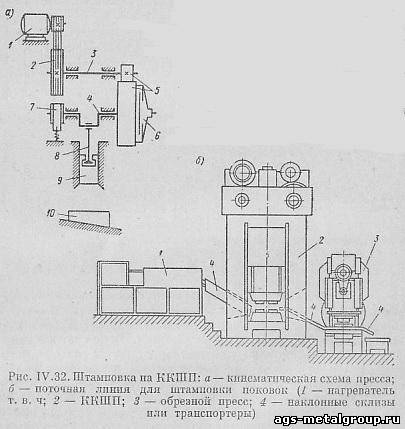
Кінематична схема ККШП показана на рис. IV.32, а. Від електродвигуна 1 через клиноременную передачу приводиться в обертання маховик 2, закріплений на валу 3. Від вала 3 рух через зубчасті колеса 5 передається кривошипному (эксцентриковому) валу 4.Останній допомогою шатуна 8 повідомляє зворотно-поступальний рух повзуна 9, на якому закріплюється верхня половина штампа.Включення кривошипно-шатунного механізму на робочий хід здійснюється пневматичної фрикційною муфтою 6, яка управляється ножною педаллю.Стрічковий гальмо 7 служить для загальмовування руху кривошипно-шатунного механізму після вимикання муфти та його зупинки при верхньому положенні повзуна. Нижня половина штампа кріпиться до столу преса 10, встановленому на похилій площині, що дозволяє змінювати його положення по висоті при установці і регулюванні штампів.
ККШП быстроходны (дають від 35 до 90 ходів в хвилину), відрізняються великою міцністю і жорсткістю станини, мають верхній і нижній виштовхувачі для примусового видалення поковок з штампів, що дозволяє знижувати штампувальні ухили до 2 - 3'. Деформування металу в кожному струмку штампа проводиться за один хід повзуна, а не за кілька ударів, як при штампуванні на молоті. Разом з тим число ходів повзуна в хвилину приблизно дорівнює числу ударів баби еквівалентних молотов, тому вдвічі і більше підвищується продуктивність штампування.
Сталість довжини ходу повзуна і плавне, без бічних зсувів рух повзуна з верхньою половиною штампа по напрямних забезпечують високу точність штампування. Преси виготовляються з зусиллям 500 - 8000 Т (4,9 - 78,5 МН), що еквівалентно масам падаючих частин паровоздушного штампувального молота 0,5 - 8 т.
Струмки штампів виконуються у вигляді вставок, циліндричних або призматичних, закріплених у спеціальних державках (пакетах).Кожну державку можна застосовувати для штампування ряду поковок, відповідно змінюючи вставки. Нижня і верхня плити державки (рис. IV.ЗЗ, б) кріпляться болтами відповідно до столу і повзуна преса. Строката струмкова вставки кріпляться в гніздах плит сталевими прихватами або хомутами, затягиваемыми болтами або клинами.
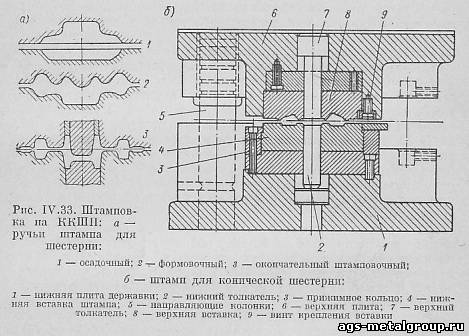
Особливості технології штампування на ККШП полягають у наступному:
1. Застосування подкатных і протяжних струмків на пресі не раціонально через сталості ходу повзуна і неможливість зміни робочого зусилля, тому зазначені заготівельні переходи повинні виконуватися на іншому агрегаті, наприклад в кувальних вальцях.
2. При штампуванні на пресі метал інтенсивніше розтікається в сторони і гірше, ніж на молотах, заповнює рельєф порожнини штампа на висоті. Тому для забезпечення поступового формоутворення поковки і полегшення заповнення остаточного струмка рекомендується розчленовувати процес штампування навіть простих за формою деталей, наприклад шестерень, на два-три переходу (рис. IV. 33, а).При цьому попередній перехід полегшує заповнення форми порожнини подальшого переходу, як би замінюючи послідовну деформацію металу в одноручьевом молотовом штампі за кілька ударів молота.
3. Бажані застосування безокисного нагріву заготовок або їх очищення від окалини перед укладанням в штамп, так як окалина у зв'язку з ненаголошеній роботою преса заштамповывается в поковку, а не відшаровується від неї.
Штампування на гвинтових фрикційних пресах. Ці преси застосовують для штампування невеликих поковок із сталі і кольорових сплавів (болтів, баранчиків, клапанів та ін) в дрібносерійному і серійному виробництві. Вони порівняно тихоходны (Vp = 0,3 ÷ 0,5 м/с), що забезпечує якісну штампування на них сплавів, чутливих до високих швидкостей деформації.
Гвинтові преси не мають фіксованого ходу повзуна, чим виключається можливість роботи в розпір і заклинювання преса. Ця обставина вигідно відрізняє їх від кривошипних пресів і дозволяє широко застосовувати штампування в закритих штампах.
Штампування на фрикційних пресах здійснюється за рахунок кінетичної енергії, накопляемой обертовим маховиком з гвинтом і рухається поступально повзуном. Фрикційні преси випускаються із зусиллям 40 - 630 т (392 - 6180 кН), а іноді і до 2000 т (19620 кН).
Штампи для фрикційних пресів зазвичай одноручьевые, відкритого чи закритого типів. Верхня частина штампа (пуансон) кріпиться хвостовиком і притискним болта в отворі повзуна преса, а нижня частина (матриця) - болтами і планками на столі преса.
Штампування на гідравлічних пресах. За останні роки значно розширилося виробництво і застосування легких сплавів. Для штампування великогабаритних деталей з таких сплавів успішно застосовують надпотужні гідравлічні штампувальні преси.
Найбільший у світі штампувальний прес зусиллям 75 000 т (736 МН) був побудований на вітчизняних заводах.
Типові та великогабаритні поковки з легких сплавів мають вигляд плоских тонкостінних деталей або видовженої прямокутної в плані форми з різним поєднанням тонких ребер жорсткості - поздовжніх, поперечних або променеподібно спрямованих. Площа проекції таких поковок досягає 3 м2, а довжина іноді перевищує 8 м при масі понад 1000 кг.
На гідропресах штампують також ребристі поковки у вигляді тіл обертання. Штампування таких поковок виконується за два-три переходи.
§ 24. Технологія штампування на горизонтально-кувальних та інших машинах
Штампування на горизонтально-кувальних машинах (ГКМ). Найбільш широко КГМ застосовуються у великосерійному і масовому виробництві для штампування деталей, що мають переважно форму тіл обертання, ускладнених бічними відростками, поднутрениями, наскрізними отворами і т. п. (рис. IV.34, а).
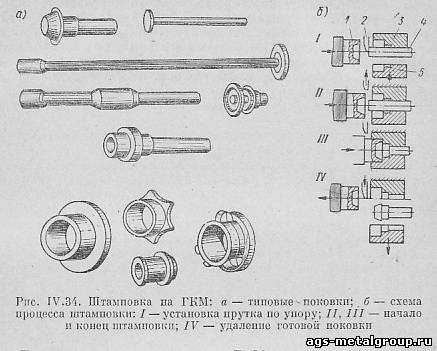
Схема процесу штампування на ГКМ дана на рис. IV. 34, б. Штампування проводиться звичайно методом висадки нагрітого кінця прутка 4, частина якого затиснута між нерухомою 3 і рухомий 5 матрицями, або ж з мірною заготовки, утримуваної кліщами з заднім упором в корпус матриці. Высаживаемая частину заготовки довжиною не більше 2,5 - 3 діаметрів дроту (при вільній осаді в одному струмку) встановлюється по упору 2 і при штампуванні заповнює робочі порожнини пуансона 1 і матриць 3 і 5.
Якщо обсяг штампуемой головки поковки перевищує 2,5 - 3 діаметра прутка, то штампування виробляють в декількох струмках многоручьевого штампа, поступово набираючи метал, причому порожнину матриці або пуансона на перших переходах не повинна перевищувати по діаметру 1,25 - 1,5 діаметрів вихідного прутка. В іншому випадку можливий поздовжній вигин заготовки, що приводить до затискачів металу і шлюбу поковок. Максимальна довжина яку висаджують частини прутка при многопереходной висадці не повинна перевищувати 12 її діаметрів.
При штампуванні кілець метал набирається висадкою, а потім у завершальному струмку проводиться наскрізна прошивка.
Переваги штампування на ГКМ: висока продуктивність, досягає 200 і більше поковок в годину; можливість штампування поковок з бічними кільцевими виступами і западинами завдяки наявності двох площин рознімання штампів (один роз'єм між матрицями, інший - між зімкнутими матрицями і пуансоном); можливість штампування без облоя, і майже без штампувальних ухилів, а також отримання поковок з наскрізними отворами (що недосяжно на інших штампувальних агрегатах). Кінематична схема ГКМ зображена на рис. IV.35.Маховик машини G приводиться в рух від електродвигуна через ремінну передачу. Він вільно обертається на приймальному валу і з'єднується з ним при включенні пневматичної фрикційної муфти F. Від приймального валу рух через зубчасті колеса z₁ і z₂ передаються кривошипному валу 3, а від нього через шатун 2 головному повзуна 1, на торці якого кріпляться пуансони. На кінці колінчастого вала насаджені ексцентрики 4, які при повороті по черзі натискають на ролики. Осі роликів закріплені в коробчатої обоймі, пов'язаної з боковим повзуном 5.Останній впливає на важільний механізм б закриття і відкриття матриць 7 і 8. Матриця 7 є рухомою, а матриця 8 - нерухома, вона закріплена на станині машини.
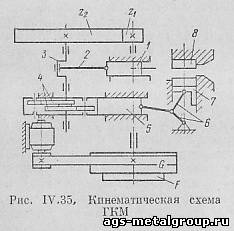
ГКМ випускаються з номінальним зусиллям від 100 до 3150 т (981 - 30 870 кН) для штампування поковок із прутів діаметром 12,5 мм (1/2") до 250 мм (10").
Зусилля Р штампування на ГКМ знаходять за формулою , де с - коефіцієнт, що залежить від конфігурації поковки; для наближених розрахунків його приймають рівним 5; F - площа проекції поковки на площину, перпендикулярну до напрямку деформуючого зусилля; - межа міцності металу при температурі штампування.
Штампування на спеціальних машинах. Горизонтально - машини вигинальні - бульдозери представляють собою горизонтальні кривошипні преси з номінальним зусиллям 30 - 500 т (294 - 4900 кН). Вони применяготся для гнуття різних деталей (хомутів, скоб, гаків і т. п.) із сортового прокату в холодному або гарячому стані за один або декілька переходів. Згинальні штампи складаються з пуансона та матриці, що прикріплюються до повзуна і упорів станини машини. Завдяки великому ходу повзуна і значного штамповому простору бульдозери призначені для згинання великогабаритних виробів.
|
Категорія: Технологія металів | Додав: 25.09.2016
|
Переглядів: 3388
| Рейтинг: 0.0/0 |
|