Статистика |
---|
Онлайн всього: 1 Гостей: 1 Користувачів: 0
|
|
43. Контроль якості та техніка безпеки при зварюванні
§ 39. Напруження і деформації при зварюванні
При зварюванні відбувається місцевий нагрів металу часто до його розплавлення, внаслідок чого метал у цих місцях прагне розширитися. У зв'язку з тим що навколишній холодний метал заважає розширенню, створюються пластичні деформації і внутрішні напруження, що викликають загальну і місцеву деформації виробу.
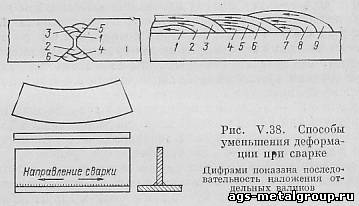
Зменшення деформації металу при зварюванні досягається різними заходами:
1) зменшенням ваги наплавленого металу шляхом зменшення перерізу швів за рахунок більшої глибини провару при використанні значної сили струму;
2) більш рівномірним нагріванням виробу в процесі зварювання (рис. 38) за рахунок застосування Х-подібних швів з чергуванням накладення окремих шарів з обох сторін оброблення;
3) пошарової проковуванням наплавленого металу;
4) жорстким кріпленням виробів у спеціальних пристосуваннях;
5) інтенсивним охолодженням в деяких випадках струменем води зварюваних виробів із зворотного боку або застосуванням тепловідвідних підкладок мідних або латунних.
Для виправлення отриманих при зварюванні деформацій у ряді випадків застосовують термічну правку вироби шляхом місцевого нагріву деталі після зварювання, що викликає зворотну деформацію виробів.
Для зняття залишкових напруг найбільше поширення має подальша термічна обробка (для сталей при 600 - 680' С), хоча можливе зняття напруг пробної навантаженням та іншими способами.
§ 40. Контроль якості зварювальних робіт
До основних дефектів зварних швів, виконаних зварюванням плавленням, відносяться наступні.
Непровари - відсутність сплавлення наплавленого металу з металом вироби з-за недотримання режимів і техніки зварювання: застосування недостатнього або надлишкового струму, малої потужності газового пальника або ж занадто швидкого переміщення електрода або пальника по шву.
Підріз - поглиблення вздовж шва на основному металі, що утворюється із-за неправильного підбору режиму зварювання.
Перегрів металу і його перепал - місцеве окислення металу в зоні зварювання з-за наявності сильноокислительной середовища, застосування великої величини струму або потужності газового пальника при повільному переміщенні електрода, газової пальники уздовж шва.
Пропалення - наскрізне проплавлення зварюваних виробів через застосування великої сили струму для певної товщини металу або великої величини зазорів.
Пористість - наявність газових раковин, свищів, шорсткості на поверхні шва у зв'язку з виділенням газів з металу, що викликається наявністю вологи у флюсі, іржею на поверхні оброблення кромок виробів і іншими причинами.
Шлакові включення - освіти, що з'явилися з-за вмісту неметалевих включень в металі або підвищеної в'язкості шлаку.
Тріщини, що виникають в металі шва або крихких навколошовних зонах внаслідок нерівномірного нагрівання й охолодження металу, поля напружень і деформацій у виробі, підвищеної концентрації водню в швах.
Жолоблення - наслідок місцевого нагріву металу в зоні зварювання.
Контроль зварювальних робіт проводять різними способами в залежності від вимог, що пред'являються до зварюваного виробу.
Для виявлення дефектів зварювання проводять зовнішній огляд шва, вимірювання розмірів шва. Міцність зварних з'єднань визначається механічними випробуваннями спеціально виготовлених зварних зразків - свідків, а іноді і зразків, вирізаних з самої деталі.
Для визначення щільності шва виробу (баки, резервуари та ін) піддають гідравлічному випробуванню. Щільність шва менш відповідальних виробів перевіряється гасом, яким змочують поверхню шва, а його зворотний бік обмазують крейдою. При наявності в металі навіть дрібної пористості гас утворює на крейдяній стороні помітна пляма. Для виробів відповідального призначення (котлів, повітряних резервуарів і ін) випробування на щільність шва виробляють нагнітанням води в виріб під тиском, що перевищує робочий в 1,25 - 1,5 рази.
Зовнішні, а також внутрішні вади на невеликій глибині виявляються способом магнітного контролю (магнітна дефектоскопія). При магнітному способі контролю поверхню металу намагничивают і посипають порошком залізної окалини. При наявності тріщин або дефектів на глибині до 5 мм у дефектних місць відбувається скупчення порошку. Дефектоскопам можна виявити зовнішні вади і внутрішні на глибину до 20 - 25 мм.
Якість зварних з'єднань відповідальних виробів (котли високого тиску, авіаційні деталі та ін) перевіряють найбільш досконалим способом - просвічуванням шва рентгенівськими або гамма-променями. Цей спосіб заснований на різній мірі проходження короткохвильових електромагнітних коливань через суцільний метал і неметалеві включення. Через дефекти шва (тріщини, раковини) такі промені проходять інтенсивніше, ніж через суцільний метал, в результаті чого на спеціальній фотоплівці утворюється почорніння, що відповідає характеру дефекту.Рентгенівськими променями контролюється якість сталевих виробів завтовшки до 100 мм, а гамма-променями - до 300 мм.
Ультразвуковий контроль заснований на перетворення електричних коливань в механічні п'єзоелектричним генератором, в якому джерелом механічних коливань служить кварцова пластинка, стискати або розтискати відповідно з частотою струму. При наявності у шві неметалічних включень ультразвук відбивається і вловлюється шукачем, перетворюючись в електричну енергію. Від шукача струм після підсилення подається на электроннолучевую трубку, в якій можна спостерігати піки того чи іншого розміру, що вказують на наявність пороку в шві.
§ 41. Техніка безпеки
При проведенні зварювання необхідно дотримуватися наступні основні правила з попередження нещасних випадків.
Від ураження струмом:
1) ретельно заземлювати зварювальні машини, трансформатор і робочий стіл зварника;
2) забезпечувати справність електропроводів; проводи повинні бути надійно ізольовані і захищені від механічних ушкоджень;
3) всі знаходяться під напругою частини электрододержателей повинні бути добре захищені від випадкового дотику;
4) після закінчення роботи або на час перебування зварника від робочого місця електричний струм повинен бути вимкнений;
5) при проведенні зварювання в сирих приміщеннях або при зварюванні металевих резервуарів, великих металоконструкцій користуватися дерев'яними підмостками, гумовими килимками для ізоляції тіла зварника від землі.
6) у разі поразки працюючого електричним струмом необхідно, не торкаючись потерпілого, вимкнути струм і надати попомощь потерпілому (робити штучне дихання).
Від ураження променями електричної дуги:
1) закрити обличчя і шию щитком або шоломом зі спеціальними темними стеклами і надягнути рукавиці;
2) огородити місце зварювання кабінами, переносними щитами для захисту від випромінювання зварювальної дуги оточуючих людей;
3) попередити оточуючих людей про початок зварювання;
Від опіків краплями розплавленого металу і шлаку:
1) працювати в комбінезоні з міцної матерії або в брезентових куртці і брюках навипуск. При автоматичної зварюванні працювати в гумових калошах і гумових рукавичках;
Від вибухів судини і вибухонебезпечних речовин:
1) не проводити зварювання судин, що знаходяться під тиском,
2) зварювання тари, резервуарів з-під нафтопродуктів проводити після попереднього очищення їх шляхом промивання гарячою водою і пропарювання пором протягом декількох годин, або після промивання 10 - 20-відсотковим розчином каустичної соди і подальшої продувки. Отвори в таких резервуарах при заварці повинні бути відкритими;
3) видалити з зварювального приміщення легкозаймисті речовини - гас, бензин тощо;
4) не робити зварювальних робіт поблизу (ближче 5 м) легкозаймистих і вибухонебезпечних речовин;
5) ретельно стежити за тим, щоб на кисневу апаратуру не потрапляло масло або жири;
6) при виявленні під час роботи нещільностей у вузлах пальника або різака слід негайно погасити полум'я і усунути нещільність;
7) при зворотних ударах або частих хлопках, що викликаються нагріванням або засміченням мундштука, необхідно швидко закрити спочатку ацетиленовий, потім кисневий вентиль і занурити пальник у воду;
8) не відігрівати замерзлі вентилі полум'ям пальника або іншим джерелом відкритого полум'я;
9) балони, наповнені газами, повинні перебувати у вертикальному положенні і їх слід прикріпити до стіни хомутами або ланцюгами.
Для видалення шкідливих газів і пилу з робочих місць зварювання і для подачі чистого повітря необхідно мати припливно-витяжну вентиляцію.
Витяжною вентиляцією при дуговому зварюванні повинна видалятися з зварювального приміщення 4000 - 6000 м3 повітря на 1 кг витрачених електродів, а при газовій зварці або кисневому різанні - 1000-1500 м3/год на 1 м3 витрачається ацетилену.
|
Категорія: Технологія металів | Додав: 26.09.2016
|
Переглядів: 2767
| Рейтинг: 0.0/0 |
|