§ 11. Хімічні процеси виробництва сталі
Хімічний склад передільного чавуну характеризується підвищеним вмістом у ньому вуглецю та інших домішок. Передільний чавун містить: 3,5 - 4,2% вуглецю, 0,2 - 1,75% кремнію, 0,5 - 1,75% марганцю, до 0,08% сірки і до 0,07% фосфору. Сталь відрізняється від чавуну більш низьким вмістом вуглецю та інших домішок і найчастіше містить 0,05 - 1,5% вуглецю, до 0,5% кремнію, 0,5 - 0,8% марганцю, до 0,05% сірки до 0,05% фосфору.
Головною метою сталеплавильного процесу є видалення містяться в чавуні надлишкових домішок за допомогою окисно-відновних процесів, що протікають в сталеплавильних агрегатах.
У сталеплавильних печах кисень найбільш швидко окисляє залізо, концентрація якого значно перевищує концентрацію інших елементів у сплаві: 2Fe + O2 = 2FeO + 63 000 кал (264,1 кДж).
Утворюється закис заліза добре розчинна як у металі, так і в шлаку і відіграє роль головного носія кисню. Атмосферний кисень окисляє шлаки, а з шлаку надходить у виді закису заліза в метал. Будь-яке підвищення змісту кисню в шлаку супроводжується збільшенням його вмісту в металі. Кремній, марганець, вуглець і інші домішки сталі володіють більш високою спорідненістю до кисню, ніж залізо, і тому вони відбирають кисень у заліза, відновлюють його, а самі окислюються (вигорають). Рідкі оксиди цих елементів спливають і потрапляють в більш легкий шлак, покриває метал;газоподібні оксиди йдуть в атмосферу або, з'єднуючись з іншими окислами, утворюють рідкі речовини, також потрапляють у шлак. Окислення домішок йде за рахунок газоподібного кисню, а також закису заліза по реакціях
Si + О2 = SiO2; Si + 2FeO = SiO2 + 2Fe
Mn + 1/2 O2 = Mn; Mn + Fe = Mn + Fe
2С + О2 = 2СО; З + FeO = З + Fe
ЗІ + 1/2 О2 = СО2
2Р + 2 1/2 О2 = Р2О5; 2Р 5FeO = Р2О5 + 5Fe
Р2О5 + 3FeO = (FeO)3•P2O5
Фосфор є шкідливою домішкою стали, так як повідомляє їй крихкість (хладноломкость) при кімнатних і особливо низьких температурах.Тому видалення фосфору - важливе завдання при виплавці сталі. Утворюється при згорянні фосфору газоподібний ангідрид Р2О5 і його нестійке з'єднання із закисом заліза важко видаляти з печі, так як при певних умовах фосфор відновлюється, переходить в метал і насичує його. Надійне видалення фосфору досягається тільки в основних сталеплавильних печах, футерованих основними вогнетривами.В такі печі без побоювання роз'єднання їх стінок завантажують вапно, яка пов'язує фосфор в міцне хімічна сполука і переводить його у шлак:
(FeO)3•Р2О5 + 4СаО = (СаО)4•P2O5 + 108 340 кал (453,9 кДж).
Однак і це хімічна сполука при високих температурах може віддавати фосфор в метал. Тому після утворення высокоосновного фосфористого шлаку його видаляють з сталеплавильних печей.
Сірка, будучи шкідливою домішкою стали, повідомляє їй підвищену крихкість (червоноламкість) при високих температурах. Видалення сірки можливо тільки в основних печах за рахунок добавок вапна та отримання шлаків високої основності:
FeS + СаО ↔ CaS + FeO - 4380 кал (18,4 кДж);
MnS + СаО ↔ CaS + MnO - 7800 кал (32,7 кДж).
Підвищення вмісту вапна обумовлює протікання цих реакцій в напрямку зліва направо, а підвищення вмісту FeO в шлаку або МпО - протягом цих реакцій у зворотному напрямку. Зниження вмісту сірки в сталі досягається особливо добре в електричних печах застосуванням відновлювальних карбідних шлаків, що містять графіт або карбід кальцію:
FeS + СаО + З = CaS + Fe + CO; MnS + СаО + З = CaS + Mn + СО; 3FeS + СаС2 + 2СаО = 3 fe + 3CaS + 2СО; 3MnS + СаС2 + 2СаО = 3Mn + 3CaS + 2СО.
Закис заліза, що грає роль носія кисню у сталеплавильних печах, необхідна в період вигоряння домішок. Однак після цього вона повинна видалятися з металу, так як подібно сірці є шкідливою домішкою, повідомляє стали червоноламкість і знижує механічні властивості. Процес звільнення стали від кисню, що міститься в ній у вигляді закису заліза FeO, називається раскислением. Цей процес є найважливішим періодом плавки і проводиться за рахунок міститься в сталі вуглецю і спеціально вводяться в сталь розкислювачів.Останні додаються в кінці плавки перед випуском сталі, так і в період випуску. Розкислення проводиться присадками в сталь феромарганцю, феросиліцію і алюмінію, які, з'єднуючись з киснем, відновлюють залізо. Отримані оксиди SiO2, MnO і Al2O3 переходять в шлак. Вуглець і марганець - найбільш слабкі розкислювачі, а алюміній найбільш сильний. Розкислення йде по реакціях
FeO + С = СО + Fe; FeO + Mn = Mn + Fe; 2FeO + Si = SiO2 + 2Fe; 3FeO + 2Al = Al2O3 + 3 fe.
Найбільш повно очищена від кисню сталь називається спокійною. Злиток такої сталі виходить щільним, без бульбашок, з зосередженою усадочною раковиною прибуткової частини зливка. Спокійна сталь може містити значні кількості вуглецю (до 2%) і виплавляється в мартенівських і електродугових печах. Поряд зі спокійної сталі у конверторах і мартенівських печах виплавляють киплячу неповністю раскисленную сталь, яка зазвичай містить мало вуглецю (0,02 - 0,3%) і розкислює тільки ферромарганцем і невеликими кількостями алюмінію.
Міститься в сталі в значних кількостях кисень при охолодженні її в изложницах взаємодіє з вуглецем. Бурхливо виділяється окис вуглецю перемішує сталь і створює видимість її кипіння. У злитку киплячої сталі замість зосередженої усадкової раковини виходить багато газових бульбашок і досі. Тому відхід від прибуткової і донної частин злитків знижується. Кипляча сталь дешевше спокійною. Вона майже не містить кремнію, добре піддається штампуванню, але більш крихка на холоді і схильна до старіння.Поряд зі спокійної і киплячої сталі виробляється і полуспокойная сталь, раскисленная меншими кількостями марганцю, кремнію і алюмінію.
§ 12. Виробництво сталі в конверторах
Виробництво сталі в кислих конверторах. В конверторах виплавляється понад 17% сталі, що випускається в нашій країні.
Кислі (бесемерівські) конвертори являють собою печі грушоподібної форми (рис. II.3, а), що складаються із сталевого кожуха з футеровкою (кладкою) з кислого динасового цегли ємністю 10 - 50 т і більше. У нижній частині конвертори мають приставні днища і повітряну коробку, через яку в конвертори вдувається ненагретый повітря під тиском 2,5 ат (0,25 МПа). Конвертор спочиває на колонах і спеціальним механізмом може обертатися навколо горизонтальної осі.Перед початком плавки конвертор встановлюють горизонтально, подають дуття, через горловину заливають рідкий бесемерівський чавун, переводять конвертор у вертикальне положення і ведуть продувку. Тепло в конверторах виходить за рахунок вигорання домішок чавуну; спеціального опалювання не потрібно. При продувці чавуну кисень повітря окислює залізо, утворює закис заліза, розчинну у металі. Наявність кисню повітря і закису заліза обумовлює вигоряння домішок чавуну: кремнію, марганцю і вуглецю по реакцій, наведених вище.Рідкі продукти реакцій спливають і потрапляють в шлак, газоподібні видаляються через горловину конвертера.
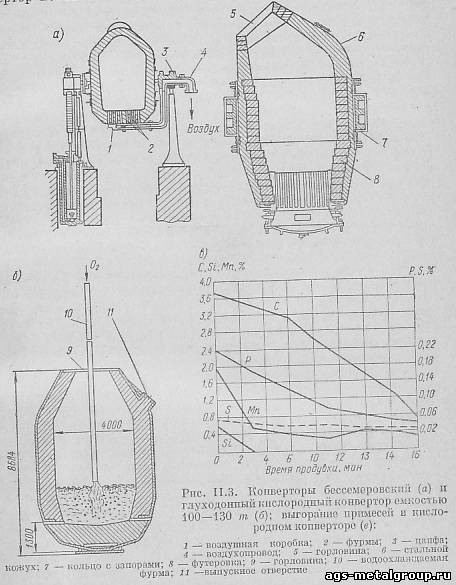
У перший період (приблизно 4 хв) інтенсивно вигорають кремній і марганець. При цьому утворюється велика кількість тепла і метал розігрівається. Особливо багато тепла утворюється при згорянні кремнію. У другий період плавки (з 4 до 10 хв) інтенсивно вигорає вуглець. Утвориться окис вуглецю по виході з горловини згорає, утворюючи довгий факел яскраво-білого полум'я. Після вигоряння вуглецю у третій період (з 10 до 12 хв) починає вигоряти залізо з утворенням бурого диму і тоді плавку припиняють. Для цього конвертор знову переводять у горизонтальне положення і припиняють дуття.Розкислюють метал присадкою феромарганцю, феросиліцію, алюмінію, добавками чавуну доводять його склад до необхідного і виливають через горловину. Весь процес плавки в залежності від перебігу процесу і ємності конвертора триває 20 - 25 хв.
Недоліками плавки сталі в конверторі з кислою футеровкою на повітряному дуття є: необхідність використання высококремнистых, чистих по сірці і фосфор чавунів, значний, вигар металу в 8 - 12%, неможливість переплавлення великих кількостей металевого брухту, а також видалення сірки і фосфору з чавуну, внаслідок чого кількість їх в бессемеровской стали виходить значно вище, ніж у мартенівської. Крім того, бессемеровская сталь при продуванні повітря сильно насичується азотом, вміст якого досягає 0,012 - 0,015%.У зв'язку з цим в конверторах на повітряному дуття отримують сталь звичайної якості, яка порівняно з якісною сталлю володіє зниженою ударною в'язкістю, підвищеної хладноломкостью, найгіршою зварюваністю і підвищеною схильністю до старіння.
Киснево-конверторний спосіб виробництва сталі. Основний метод конвертерного переділу чавуну на сталь в даний час - плавка сталі в основних глуходонных конверторах з продувкою зверху технічно чистим киснем. Ємність таких кисневих конверторів - 30, 50 і 100 - 130 т. Ємність їх передбачається збільшити до 250 - 350 т. Кладка конверторів основна - смолодоломитовая або магнезитохромитовая. Як видно з рис. II.3, б, кисневий конвертор має симетричну форму, глухе знімне дно і зверху випускний отвір для сталі.У таких конверторах можуть перероблятися чавуни з широкими коливаннями хімічного складу, але частіше переробляються рідкі мартенівські чавуни. Крім чавуну в конвертори завантажують до 30% металевого брухту, залізну руду і флюси - вапно, боксит і плавиковий шпат. Технічно чистий кисень під тиском до 12 ат (1,2 МПа) подається зверху через водоохолоджувальну фурму на дзеркало рідкого металу. За рахунок кисню і закису заліза відбувається інтенсивне вигоряння кремнію, марганцю і фосфору (рис. II.3, в).Температура металу в зоні дії кисню досягає 3000' З, і весь метал в конверторі сильно розігрівається. Зниження температури металу досягається введенням охолоджувачів - брухту, руди та флюсів. Вуглець спочатку вигорає повільно, а після розігріву металу вигоряння його прискорюється. Контроль за змістом вуглецю проводиться спектральним методом.
В основних кисневих конверторах за рахунок введення вапна і підвищеної основності шлаків досягається зниження вмісту в сталі фосфору і сірки. Тривалість продувки в 100-тонному конверторі становить 14 - 18 хв, а загальна тривалість плавки 45 хв. В кінці плавки метал доводиться до заданого складу, розкислює й випускається через бічний отвір, а шлак - через горловину. У кисневих конверторах отримують сталь з низьким вмістом азоту, сірки і фосфору як звичайної якості, так і якісну, по своїм властивостям не поступається мартенівської сталі.Крім вуглецевих сталей виплавляються низьколеговані і в якості досвіду леговані сталі. Питомі капітальні витрати на будівництво конверторних цехів на 35% нижче, ніж на будівництво мартенівських цехів. Собівартість конверторної сталі на 3,5% нижче, ніж мартенівської сталі, а продуктивність праці у конверторних цехах на 45% вище, ніж в мартенівських. Тому кислородноконверторный спосіб переділу чавуну можна вважати найбільш рентабельним і перспективним. Недоліками способу є: підвищений витрата вогнетривів і високий вигар металу.
Плавка в конверторах піддається автоматизації з використанням електронно-обчислювальних пристроїв.
Поряд з переділом чавуну на сталь в конверторах стаціонарного типу розроблені більш досконалі процеси отримання сталі в обертових агрегатах. У зв'язку з кращим перемішуванням металу, подвійний зміною шлаку ці агрегати відрізняються підвищеною продуктивністю, а виплавляється в них сталь - підвищеною якістю.
§ 13. Виробництво сталі в мартенівських печах
У мартенівських печах виплавляють близько 70% сталі. До переваг цього способу виплавки сталі відносяться: можливість використання великих кількостей металевого брухту, менш жорсткі вимоги до складу шихтових матеріалів, хороша керованість і можливість автоматизації процесів плавки, широкий асортимент і задовільну якість виплавлюваних марок сталі, підвищена точність хімічного складу, а також малий вигар металу.Недоліки способу полягають в періодичності процесу плавки, складності обладнання, а також в більш високій вартості виплавленої сталі в порівнянні зі сталлю, одержуваної в конверторах.
§ 14. Пристрій і робота мартенівської печі
Сучасні мартенівські печі великої ємності в 500 - 900 т використовуються для одержання злитків, печі малої ємності в 20 - 100 т - у виробництві фасонних виливків.

Робочий простір печі (рис. 11.4) обмежена зверху склепінням, а з боків - стінками і укосами. У передній стінці є завалочні вікна для завантаження сирих матеріалів.
Нижня частина робочого простору обмежена укосами і подом, що утворюють ванну, в якій розміщується метал. Під печі має нахил у бік отвору для випуску сталі. В залежності від виду вогнетривких матеріалів металевої ванни мартенівські печі поділяються на кислі і основні. Останні найбільш поширені на вітчизняних заводах. Ліва і права головки мартенівської печі служать для підведення пального газу і нагрітого повітря по окремих каналах, для зміщення і спалювання газу на вихід у робочий простір печі.При роботі печей на мазуті вони мають тільки два регенератора для нагрівання повітря; головка має один канал для підведення нагрітого повітря і форсунку для спалювання пального. Отримання високих температур в робочому просторі печі 1800 - 2000' З можливо тільки при використанні нагрітого повітря, а при роботі на газі - і нагрітого газу (суміші доменного, коксувального і генераторного). Нагрівання газу і повітря здійснюється в регенераторах за рахунок тепла газів, що відходять.
|